Ecole Polytechnique’s Solid Mechanics Laboratory
Joint with control stiffness
Electro-magnetic particles brake
Goal
Research, design, produce and test a new design of electro-magnetic joint with controlled stiffness (brake with controlled braking torque) based on a magnetorheological fluid technology.
This technology could advantageously replace other brake/clutch technologies in many applications thanks to:
> high braking torque/weight and braking torque/volume ratios,
> high controllability: torque accurately controlled by tension control, fast response and wide range of linear behavior
It can moreover be used to build rotary buttons with haptic feedback: force feedback patterns can be programmed and adjusted instantaneously.
Rather than focusing on building a specific application, the goal of the project was to maximize the torque over volume ratio of the joint for a given volume.
The product consists of a stack of disks, alternatively fixed to the rotor and stator of the joint, with magnetorheological fluid filling the gaps between them. When subjected to a magnetic field created by a coil, the fluid greatly increases its apparent viscosity, to the point of becoming a viscoelastic solid, completely linking the rotor and stator together.
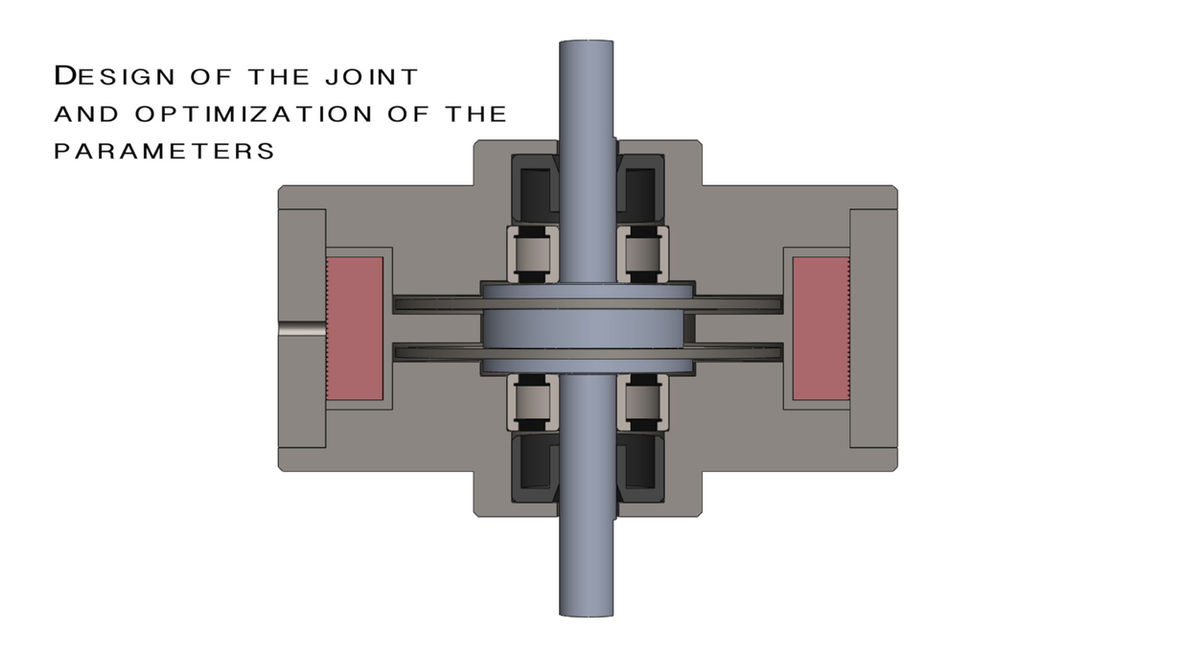
Electro-magnetic brake
Role & contribution
-
Electromechanical design and dimensioning of the brake, including magnetic circuit and sealed rotary joint design - CAD modeling
-
Magnetic flux, heat and stress simulation; optimization of the system performance (braking torque/volume)
-
GD&T, fabrication, assembly
-
Custom test bench design and fabrication, characterization of the system performance
Outcome

Successfully designed, produced and characterized the brake.
-
Braking torque achieved ranges from a torque as low as 0.01Nm when the device is not powered, to 3Nm when powered by a current of 3A.
-
Improved braking-torque/weight ratio by more than 60% compared to a benchmark one-disk design.
Learnings
-
Electromechanical device design (including magnetic circuit design, coil design, heat dissipation considerations, magnetorheological fluid use)
-
Rotary joint design (ball bearing assembly, rotary sealing solutions)
-
Multiphysics simulation and optimization
-
Small batch metal manufacturing and prototyping
-
Test bench design and device performance characterization







